Escalator Components
1.Top and bottom landing platforms
These two platforms house the curved sections of the tracks, as well as the gears and motors that drive the stairs. The top platform contains the motor assembly and the main drive gear, while the bottom holds the step return idler sprockets. These sections also anchor the ends of the escalator truss. In addition, the platforms contain a floor plate and a comb plate. The floor plate provides a place for the passengers to stand before they step onto the moving stairs. This plate is flush with the finished floor and is either hinged or removable to allow easy access to the machinery below. The comb plate is the piece between the stationary floor plate and the moving step. It is so named because its edge has a series of cleats that resemble the teeth of a comb. These teeth mesh with matching cleats on the edges of the steps. This design is necessary to minimize the gap between the stair and the landing, which helps prevent objects from getting caught in the gap.
2.The truss
The truss is a hollow metal structure that bridges the lower and upper landings. It is composed of two side sections joined together with cross braces across the bottom and just below the top. The ends of the truss are attached to the top and bottom landing platforms via steel or concrete supports. The truss carries all the straight track sections connecting the upper and lower sections.
3.The tracks
The track system is built into the truss to guide the step chain, which continuously pulls the steps from the bottom platform and back to the top in an endless loop. There are actually two tracks: one for the front wheels of the steps (called the step-wheel track) and one for the back wheels of the steps (called the trailer-wheel track). The relative positions of these tracks cause the steps to form a staircase as they move out from under the comb plate. Along the straight section of the truss the tracks are at their maximum distance apart. This configuration forces the back of one step to be at a 90-degree angle relative to the step behind it. This right angle bends the steps into a stair shape. At the top and bottom of the escalator, the two tracks converge so that the front and back wheels of the steps are almost in a straight line. This causes the stairs to lay in a flat sheet-like arrangement, one after another, so they can easily travel around the bend in the curved section of track. The tracks carry the steps down along the underside of the truss until they reach the bottom landing, where they pass through another curved section of track before exiting the bottom landing. At this point the tracks separate and the steps once again assume a stair case configuration. This cycle is repeated continually as the steps are pulled from bottom to top and back to the bottom again.
4.The steps
The steps themselves are solid, one-piece, die-cast aluminum. Rubber mats may be affixed to their surface to reduce slippage, and yellow demarcation lines may be added to clearly indicate their edges. The leading and trailing edges of each step are cleated with comb-like protrusions that mesh with the comb plates on the top and bottom platforms. The steps are linked by a continuous metal chain so they form a closed loop with each step able to bend in relation to its neighbors. The front and back edges of the steps are each connected to two wheels. The rear wheels are set further apart to fit into the back track and the front wheels have shorter axles to fit into the narrower front track. As described above, the position of the tracks controls the orientation of the steps.
5.The railing
The railing provides a convenient handhold for passengers while they are riding the escalator. It is constructed of four distinct sections. At the center of the railing is a "slider," also known as a "glider ply," which is a layer of a cotton or synthetic textile. The purpose of the slider layer is to allow the railing to move smoothly along its track. The next layer, known as the tension member, consists of either steel cable or flat steel tape. It provides the handrail with the necessary tensile strength and flexibility. On top of tension member are the inner construction components, which are made of chemically treated rubber designed to prevent the layers from separating. Finally, the outer layer, the only part that passengers actually see, is the rubber cover, which is a blend of synthetic polymers and rubber. This cover is designed to resist degradation from environmental conditions, mechanical wear and tear, and human vandalism. The railing is constructed by feeding rubber through a computer controlled extrusion machine to produce layers of the required size and type in order to match specific orders. The component layers of fabric, rubber, and steel are shaped by skilled workers before being fed into the presses, where they are fused together. When installed, the finished railing is pulled along its track by a chain that is connected to the main drive gear by a series of pulleys.
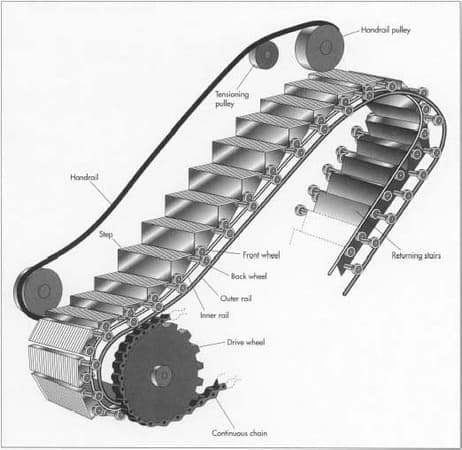
An escalator is a continuously moving staircase. Each stair has a pair of wheels on each side, one at the front of the step and one at the rear. The wheels run on two rails. At the top and bottom of the escalator, the inner rail dips beneath the outer rail, so that the bottom of the stair flattens, making it easier for riders to get on and off.